The ever-increasing push for vehicle refinement and improved driver comfort levels calls for highly sophisticated and technically advanced NVH Test Systems using chassis dynamometers within semi anechoic chambers.
Download our latest NVH Brochure (PDF), by clicking here!
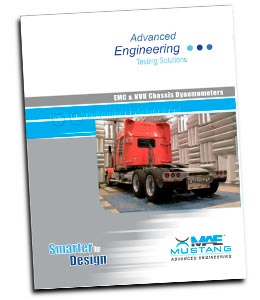
Standard Features

- Highly responsive inertia simulation capability
- Accurate and responsive roll speed synchronization
- Independent wheel control
- Emission standard road simulation accuracy
- Phase lock (relative position control) of the rolls
- “Acoustically dead” roll design and construction
The ever-increasing push for vehicle refinement and improved driver comfort levels calls for highly sophisticated and technically advanced NVH Test Systems using chassis dynamometers within semi anechoic chambers. NVH chassis dynamometer applications have long been a specialty and area of technical expertise for the team of testing and applications engineers of Mustang Advanced Engineering. Whether your application involves interior or exterior NVH challenges, MAE has an equipment and systems solution to meet your needs as well as your budget. MAE offers NVH chassis dynamometers with roll diameters ranging from 30” to 72” and offers direct HUB connection style test beds for applications that require the complete elimination of tire generated NHV. Regardless of the unique challenges of your application, MAE has an economical solution to meet your NVH chassis dynamometer testing needs.MAE is widely regarded as a leading global provider of chassis dynamometer systems for a wide range of application that require accurate and repeatable road load simulation, speed control, force control or acceleration control. Mustang’s line-up of ultra-low noise NVH chassis dynamometer systems have evolved and acquired techniques and capabilities previously only demanded in “high accuracy” emission test systems.
The latest NVH Chassis Dynamometer systems developed by MAE utilize AC Motors and provide significant benefits including:

- Highly responsive inertia simulation capability
- Accurate and responsive roll speed synchronization
- Independent wheel control
- Emission standard road simulation accuracy
- Phase lock (relative position control) of the rolls
- “Acoustically dead” roll design and construction
Roll Design
- Roll surface finish conducive to noise abatement
- Inner roll coating of a water based visco-elastic compound that reduces the structure-borne vibration.
- Roll end cap flash with roll face
Vibration Isolation
- Chassis dynamometer floor plating isolated with a elastomeric isolator which isolated noise, shock, and hi-frequency vibration
- Pit walls insulated with sound absorbing sheeting
- Chassis dynamometer frame isolated from pit with vibration isolation tri-wedge machinery mount
Bearings
- Hydrostatic bearings and special lube system
Sound Barriers
- Sound barrier encasing motor
- Sound barrier encasing rolls
- Motor drives and fan system in isolated location