The EV, BEV, PHEV, HEV, and FCEV Market
In the race to develop the next generation electric vehicle powertrain system or sub-system to satisfy all of the conflicting demands for the SAE J1634 energy consumption range test procedure, driving performance, improved fuel economy, and reduced vehicle exhaust emissions, MAE has solutions for testing and validation to meet these requirements.
Rapid BEV, HEV, PHEV, and FCEV systems development in today’s globally competitive business environment can often feel like a daunting puzzle. Solving the puzzle requires highly-sophisticated and technically-advanced testing and simulation systems to test and validate each component or sub-component independently, using Hardware-in-the-loop (HIL) simulation to take the place of missing elements of a powertrain system.
Mustang Advanced Engineering has the right resources and products to assist in the engineering, development and validation of your hybrid vehicle systems. As a leading supplier of testing and simulation solutions for the development of powertrains and powertrain components, MAE has been involved in the development of advanced HEV testing and simulation test systems from the very beginning. MAE delivered one of the industry’s first hybrid electric vehicle test systems for GM’s EV1 program in the late 1990’s. When the competition was just learning what a hybrid was, Mustang was delivering more systems for Allison Transmission’s hybrid vehicle powertrain development. MAE has continued to develop hardware and software for SAE J1634 battery electric vehicle energy consumption range test procedure, meeting EPA J1711, J2711 multi-cycle, single-cycle, 5-cycle, J1634_201707, July 2017 standard motor testing for EVs.
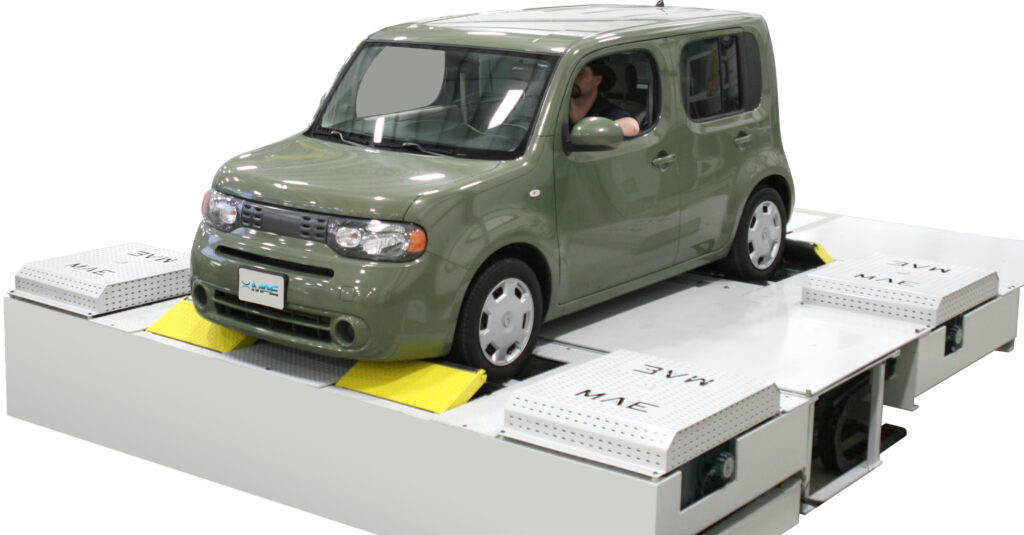